Showing results for ( results)

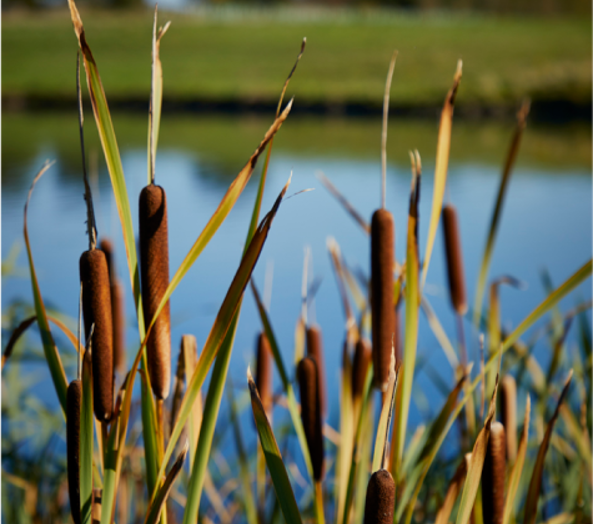
Sustainability and energy efficiency starts at home.
At Plasmor, we practice what we preach. So not only do we advise you on your building’s energy efficiency, but we also follow the same guidance in our own building projects too.
As we continue to invest in our operating sites; 2022 & 2023 has seen the construction of two new office and welfare facilities. For both new builds, we have achieved an Energy Performance Certificate rating of “A” and they have been fitted out with energy efficient technologies including air source heat pumps, under floor heating, solar thermal hot water generation and LED lighting.
This sits alongside our wall construction which uses our own thermally efficient Plasmor Block wall construction achieving, thanks to the expertise of our technical support team, a U value of 0.18 W/m2K.
And our efforts to be more sustainable don’t stop there…
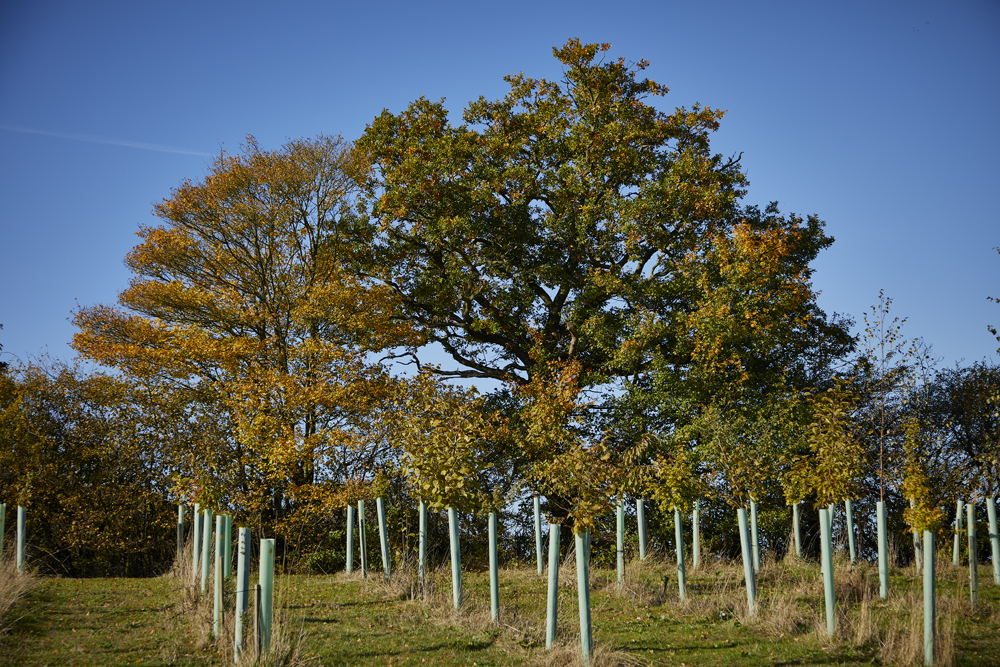
Sustainable distribution; wherever possible.
At Plasmor, we always strive to place our production plants, in strategic locations, close to the source of the raw materials we need to produce our building blocks and paving. We do this, to minimise the road journeys needed to transfer our materials from source to site. Where we can’t reduce the distance to less than 40 miles, wherever possible we’ll utilise the railways and inland waterways to keep our carbon footprint from transporting raw materials, as low as possible.
It's not just our production plants that are strategically located. Our distribution plants are also carefully considered. We strive to place our distribution plants as close as possible to densely populated, urban areas, where demand for our products is highest. This helps to keep our LGV movements to a minimum. We’re also committed to continuing our use of rail transport to distribute our products. Already 18% of our finished products are delivered by rail, every day, that’s the equivalent of taking almost 50 LGVs off the roads.
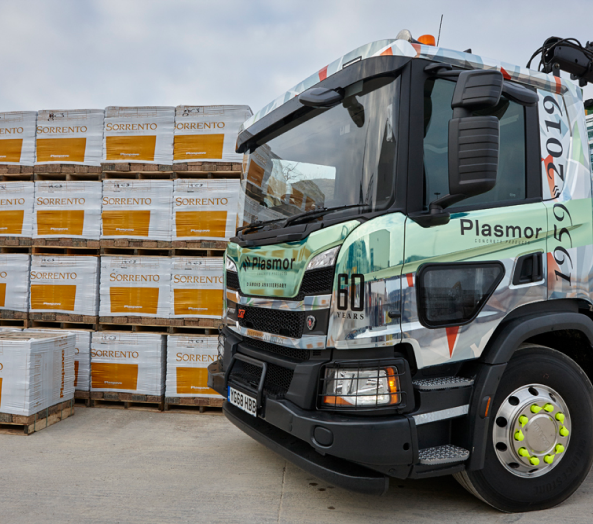
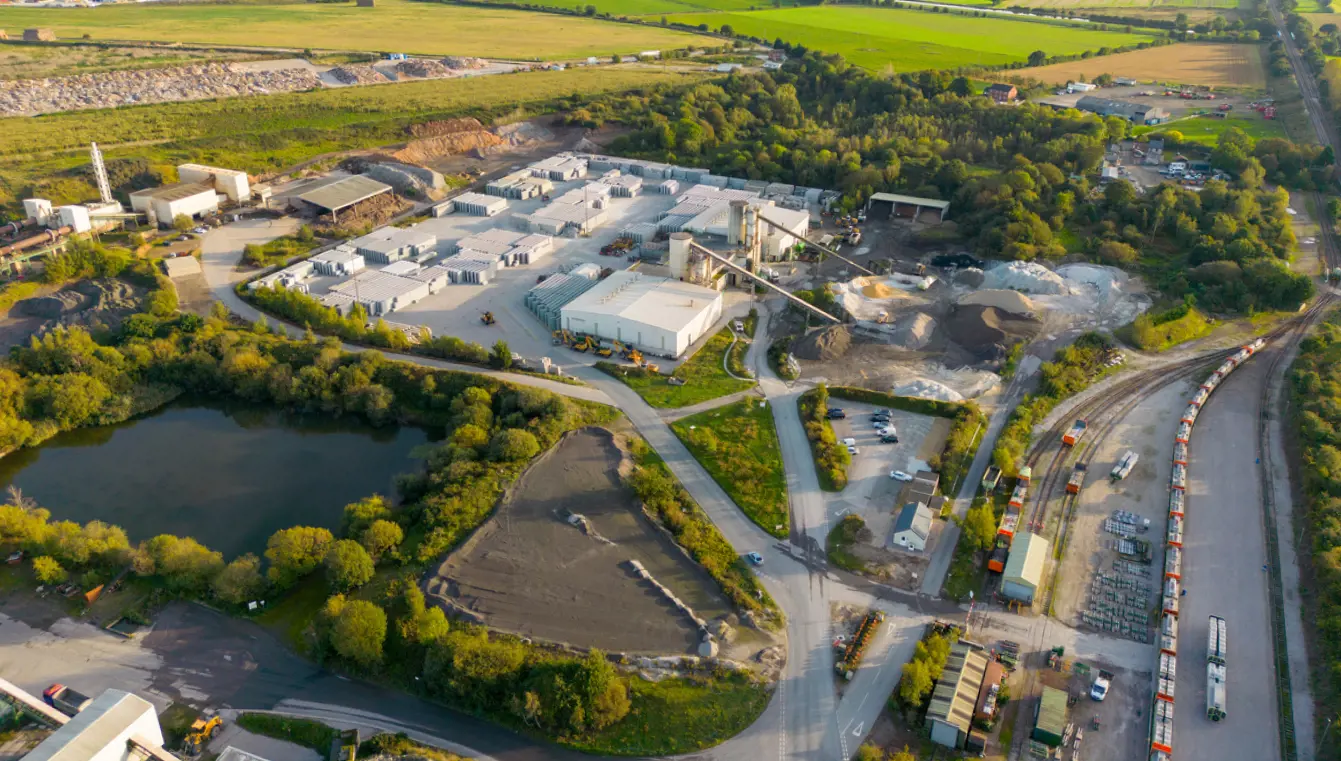
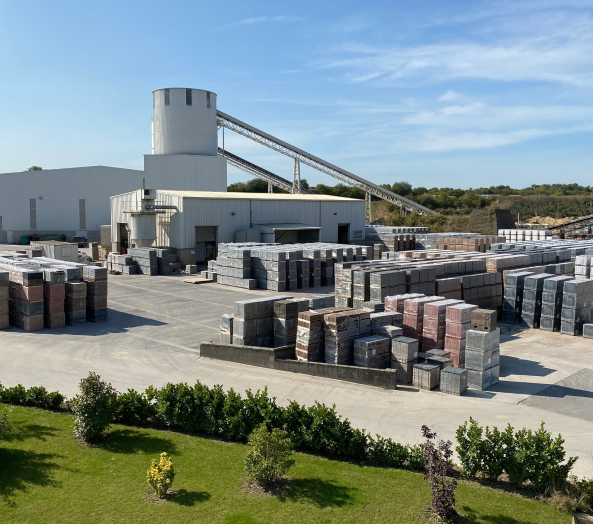
Sustainable production; now and in the future.
Where we need to use primary aggregate in the production of our building and paving blocks, we also use a significant amount of clay. The clay is uniquely processed in our state-of-the-art rotary kiln, to expand it to five times its original volume. What’s the benefit of using expanded clay in our production? Well, unlike alternative virgin quarried aggregates, such as stone, sand, and gravel, using our pioneering expanded clay process, for every one tonne of clay we quarry, we get five times as much clay in volume to use in our production process.
On top of reducing the amount of material we’re quarrying; we’re also maximising our use of recycled replacement or substitute cement products and we’re recycling and reusing all our own waste materials generated during our production process, which means we’ve reduced the waste we’re sending to landfill right down to zero.
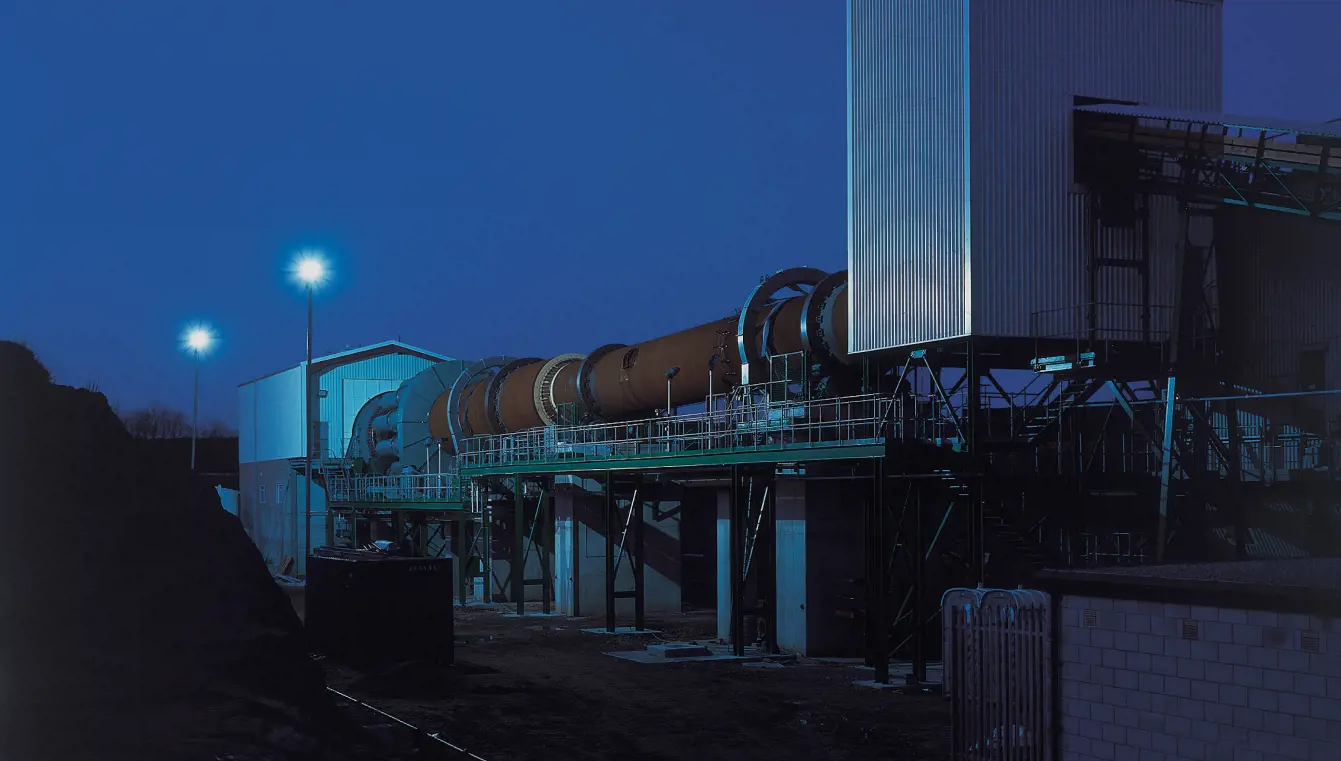
Re-wilding and regenerating our quarry sites to create a home for nature.
Quarrying is a necessary part of our production process, but even so, when the quarry site is no longer in use, we take the time to rewild these sites into a home for nature, and we like to keep a close conservationist’s eye on who moves in!
For example, at our Hemingborough site, we work closely with the RSPB and Natural England, who regularly monitor the 127 different species of bird who’ve made a home on our former quarry ponds. Local ornithologists on behalf of the RSPB have already spotted Green Woodpeckers, Corn Buntings, Little Grebes, Red Kites, Meadow Pipits and Willow Warblers to name just a few of the species feeding, roosting, nesting and moving though the site. Our brick pits are also able to support the expansion of several key species in the area too. Already two pairs of Little Ringed Plover’s (of which there are only a handful of pairs in the wider York area) have bred in 2023 – a fantastic step in the preservation of the species.
This success isn’t without planning, preparation and investment. All our quarries have comprehensive restoration plans in place for when they’re no longer in use. Since 2008 we’ve planted an amazing 8,000 trees including Field Maple, Wild Cherry, Sessile Oak and Hawthorn to name just a few, in an effort to create diverse habitats. It’s not just trees we plant either, we also sow a variety of grasses and meadow flower mixes which we leave to grow wild and the overburden, which we strip from the site initially to access the clay we need, is reused when the quarry is restored.
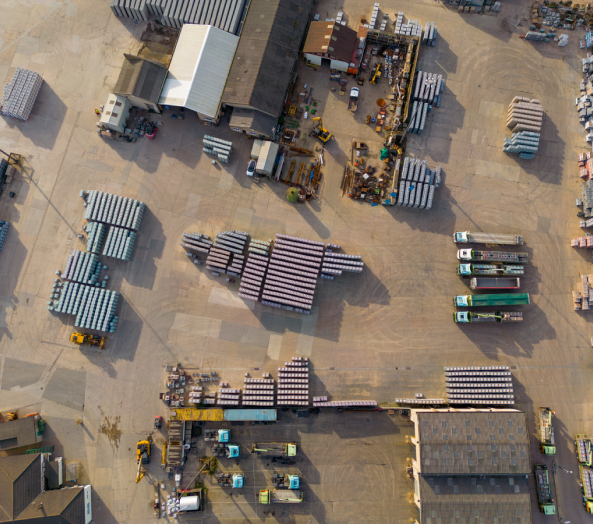
Sustainable energy, recycled stationary & environmentally friendly packaging.
It’s not just what we manufacture and how we distribute it that’s getting more sustainable at Plasmor, it’s everything we do and how we do it. We’re using alternative fuels, including waste and recycled materials, to generate the heating and power we need to run every aspect of the business.
We’re modernising all our machinery, especially our energy generation and product curing equipment, to ensure it’s more energy efficient. We’re using recycled paper for all our stationery and business forms. Our company literature if it is printed, is printed Elemental Chlorine Free on sustainably soured sheets. Our products are distributed using minimal packaging, and where there is packaging, the materials used are biodegradable or recyclable.
We’re continuously improving our supply chain management, to procure our raw materials and equipment from environmentally sensitive suppliers and renewable sources where possible. And last but by no means least, for both the environment and our neighbours, as well as Health and Safety best practice, we’re committed to monitoring and maximising air and noise suppression at our plants.
What are the next steps on our sustainability journey?
As well as reducing our mileage by road and increasing our distribution by rail, we are also working hard towards the modernisation of our LGV fleet. We’re investing in new vehicles specified and fully equipped to the latest European Emissions Standards.
We’re also working on developing new products that are lighter, to create larger transport payloads and reduce our environmental impact from vehicles even further.
And speaking of new product development, we’re also looking at more ways we can use environmentally benign materials, how we can conserve more energy and how we can use alternative waste and recycled fuel sources more and more.
We’re supporting more sustainable homes too.
Many of the building and paving blocks we produce go on to be used in lots of different buildings and projects, but often they are used to build new homes and residential buildings. That’s because Plasmor concrete blocks have excellent fire-resistant properties.
Our aggregate concrete blocks achieve high Green Guide ratings for walls and floors and concrete blocks in general cannot be attacked or weakened by vermin and insects, and even withstand adverse effects from flood water and water leaks. All of that means our blocks support builders in being compliant with The Code for Sustainable Homes.
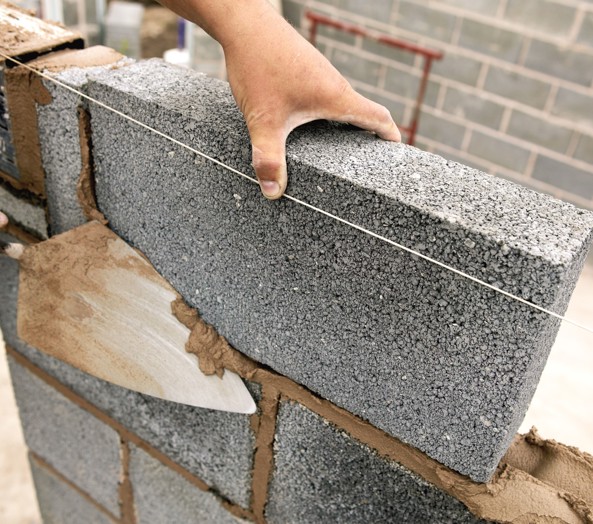
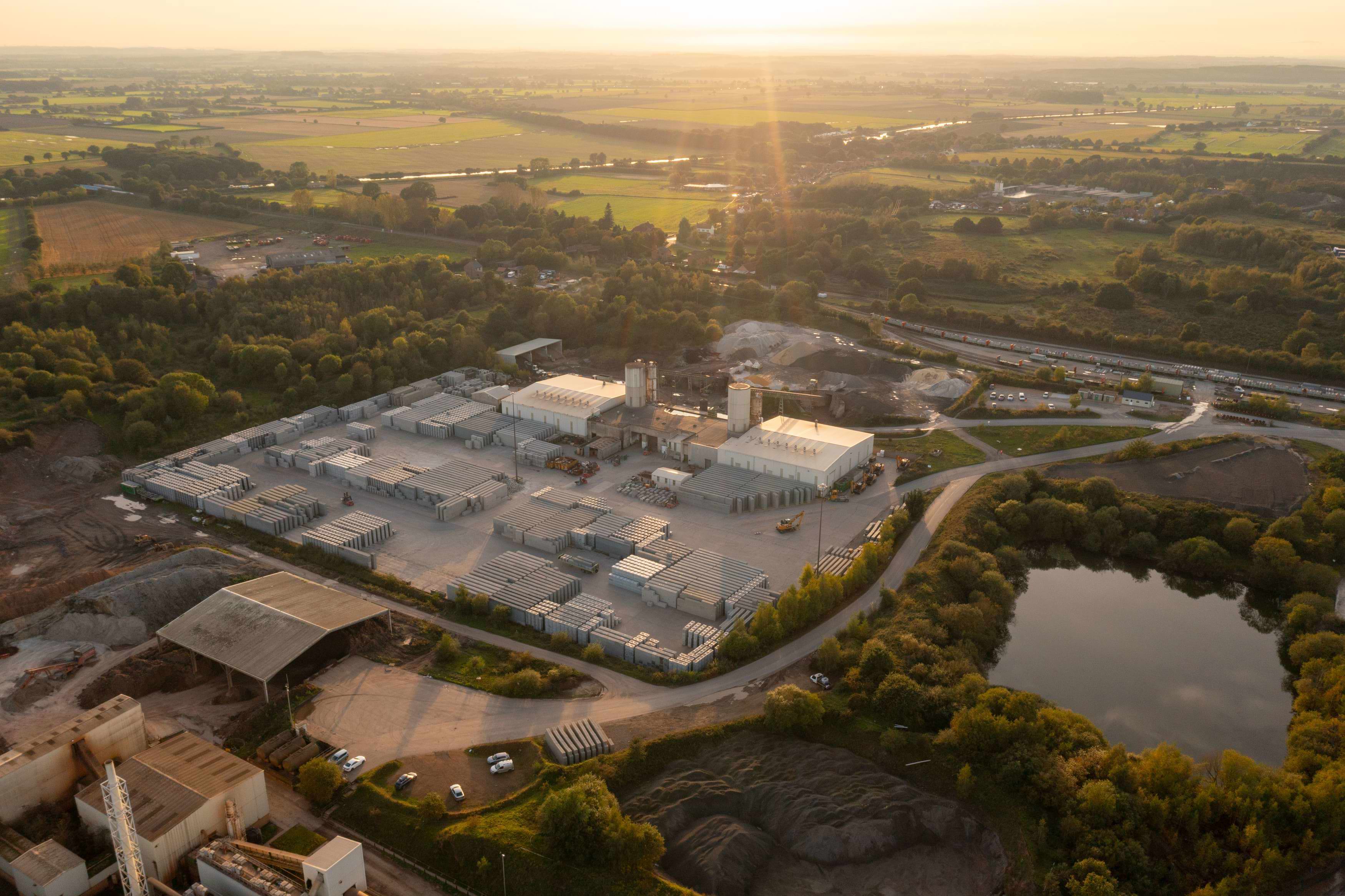